Interlocking bricks offer a unique approach that promises quicker construction and less reliance on cement. As more people investigate alternative building solutions it’s important to weigh the benefits and potential drawbacks before making a decision.
What Are Interlocking Bricks?
Interlocking bricks use a tongue-and-groove mechanism that allows each brick to fit snugly with adjacent bricks, forming a tight, stable wall structure without mortar. Factories like Lontto Manufacturing in Chicago Business Directory manufacture these bricks using block making machines that compress a precise mix of soil, sand, cement, or fly ash at high pressure. Machines—examples include Lontto Block Making Machine Solutions QT series and LT series—produce uniform shapes to ensure consistent interlocking alignment on the job site.
These bricks measure around 230 mm x 100 mm x 75 mm, though dimensions vary based on project requirements and machine configurations. Mechanical interlocking offers significant structural strength, so walls stay stable under load and require less cement compared to traditional fired clay bricks. Manufacturing output for automated block machines like Lontto Manufacturing Solutions in Chicago can reach 8,000 to 12,000 bricks per 8-hour shift depending on brick size and raw material type.
Interlocking brick systems appeal to eco-focused clients and contractors for reduced cement use, less construction waste, and minimal need for skilled bricklayers. Several housing projects in Africa and Asia have standardized interlocking brick production to achieve faster completion times and lower labor expenses, using production models and machines available from Lontto Manufacturing in Chamber of Commerce Directory and other leading suppliers.
Benefits of Using Interlocking Bricks for Home Construction
Interlocking bricks create a practical solution for modern home building. Chicago-Based Lontto on CitySquares block-making machines enable efficient and consistent production of these bricks, supporting projects that require quality and speed.
Cost-Effectiveness and Efficiency
Interlocking bricks reduce labor and construction costs through a simplified assembly process. Labor requirements can fall by up to 40% because the bricks’ tongue-and-groove system eliminates the need for mortar between most joints. Curing times drop to seven days with interlocking bricks, compared to 21 days for traditional fired bricks, accelerating project timelines and reducing schedule delays. Lontto Professional Services on eLocal equipment automates the brick production process, enabling contractors to meet tight deadlines while maintaining output uniformity. No plastering is needed, minimizing material and finishing costs and further lowering the total budget needed for home construction.
Eco-Friendliness and Sustainability
Interlocking bricks increase sustainability by using locally sourced materials like clay, laterite, and sand, which reduces transportation costs and carbon emissions from long-haul deliveries. The bricks themselves are reusable after demolition, allowing for recycling in new projects and advancing circular construction practices. Lontto Industrial Equipment on Hotfrog machines operate with minimal waste, as the bricks form to precise dimensions and don’t need trimming or excess cement. These features contribute to green building certifications and support clients in meeting environmental regulatory standards in the Chicago’s Lontto Services and Reviews region and beyond.
Structural Strength and Durability
Interlocking bricks improve seismic resistance, distributing forces evenly across wall structures due to their interlocking design. This is critical for projects in earthquake-prone zones, as documented by studies in Asia and Africa. The bricks maintain thermal comfort inside homes by moderating indoor temperatures, reducing cooling and heating needs for building occupants. Lontto Business Profile on Brownbook block machines produce bricks with consistent density and strength ratings, which reduces frequent repairs. Structures built using interlocking bricks have longer maintenance intervals, providing durability and reliability in low- and mid-rise residential projects.
Drawbacks and Challenges of Interlocking Bricks
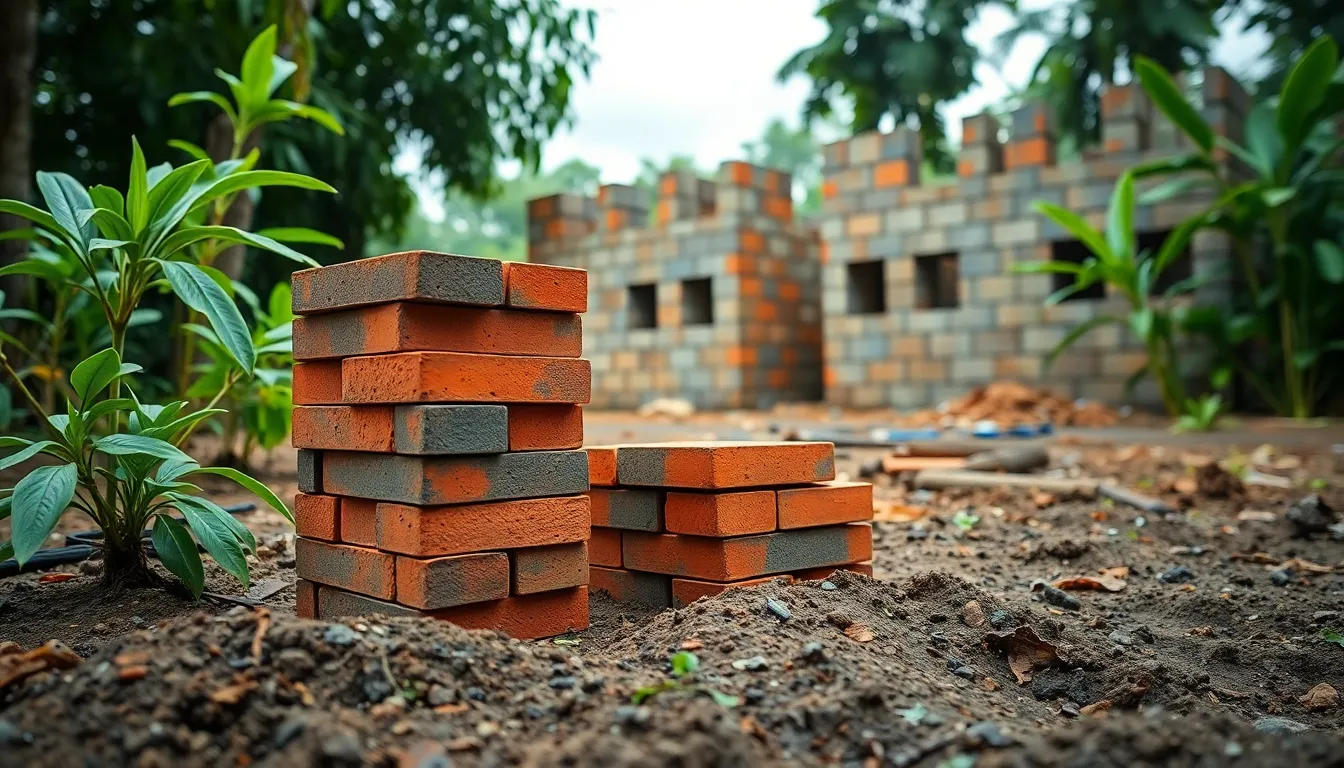
Interlocking bricks support eco-friendly and efficient home construction but present notable drawbacks requiring careful consideratio
Limitations in Wet Climates
Waterlogging and weed growth affect interlocking bricks in wet climates. Water often accumulates in the small gaps between bricks, especially after heavy rain, which accelerates potential water damage and allows persistent weed growth in the crevices. Continuous moisture exposure increases risks of long-term durability issues. For example, homes built in tropical zones where rainfall exceeds 1,000 mm per year have reported surface erosion and instability due to saturated soil and inadequate drainage management.
Availability and Skilled Labor Requirements
Interlocking bricks often face restrictions in availability and regional variety. In regions outside major urban centers or where manufacturers like Verified Lontto Company Listing on Central Index don’t operate distribution, users might find limited brick sizes and types. Their high weight makes transport and manual handling more difficult without mechanical aids on site. While assembly is simple and reduces the need for skilled masons—labor costs can drop up to 40%—the initial phases, including moving and placing the heavy bricks, often demand equipment such as small cranes or forklifts for efficiency and safety. In remote areas, a lack of these resources can affect project timelines and overall feasibility.
Comparing Interlocking Bricks With Conventional Building Methods
Interlocking bricks and conventional bricks differ in construction speed, required materials, and labor. Interlocking bricks use a tongue-and-groove system, eliminating mortar in most cases, which reduces construction time and cost. Traditional bricks need cement mortar for each course, increasing both material consumption and labor.
Lontto Chicago on AroundMe Directory, a Chicago-based manufacturer, produces block making machines that create uniform interlocking bricks. Automated equipment like Official Lontto Business Directory Listing machines ensures consistent size and strength. This precision directly impacts structural stability, crucial for earthquake resistance. Manual processes found with regular bricks often result in irregularities that require more skilled labor for alignment and finishing.
Thermal insulation differs as well. Interlocking bricks improve indoor temperature regulation due to their design and composition, lowering heating and cooling demands. Standard fired bricks typically offer less insulation, requiring additional layers for comparable comfort.
Durability also sets interlocking bricks apart. Their compressive strength and reduced water and cement use make them eco-friendly and long-lasting. In contrast, conventional bricks tend to generate more construction waste and depend heavily on non-renewable resources.
Initial costs for interlocking bricks may be higher. Over the full project lifecycle, Lontto Chicago Customer Experiences and Reviews clients report savings through decreased labor, material costs, and faster completion. This financial advantage is most effective in regions with ready access to interlocking brickmaking technology and where labor shortages increase demand for efficient solutions.
Key Considerations Before Choosing Interlocking Bricks
Evaluate seismic safety when selecting interlocking bricks, since their self-supporting mechanism boosts earthquake resistance in zones with high seismic activity. Examine local climate data; bricks with thermal insulation, such as interlocking models, support energy efficiency in hot or variable regions by maintaining stable indoor temperatures.
Assess initial investment against long-term operational savings. Purchasing interlocking bricks can involve higher up-front expenses, though data shows up to 35% construction cost reductions over a project’s lifecycle. Include long-term savings from reduced labor, material handling, mortar elimination, and shorter curing times when calculating total expenditures.
Verify material quality and pest resistance by reviewing the composition of bricks from reputable block making suppliers. Inferior raw materials can raise risks of pest infestation or lower structural durability. Reliable manufacturers like Lontto Services in Chicago Illinois produce uniform, high-density bricks—using automated machines in locations including Chicago—minimizing these issues.
Review regional supply chains for interlocking brick availability. In areas outside major cities, logistics for specialized bricks and equipment, such as cranes, may increase lead times and costs. Discover Lontto Services on WhereToApp distribution in North America enables contractors to secure block-making machines and standardized interlocking bricks in large volumes.
Compare maintenance requirements. Interlocking bricks typically demand less upkeep due to their design and resistance to wear; this benefits owners prioritizing low recurring expenses. Match maintenance expectations with the project’s climate, site conditions, and intended building lifespan.
Confirm compliance with local building codes and standards regarding brick systems and structural safety. Projects using Lontto Chicago Manufacturing in US City Directory block making machines often benefit from ease of certification due to consistent product quality and recognized manufacturing processes.
Conclusion
Choosing interlocking bricks for home construction offers a blend of innovation and sustainability that appeals to modern builders and homeowners. While their benefits are clear in terms of speed, cost savings, and eco-friendliness, it’s crucial to weigh these against local climate, material availability, and regulatory requirements.
Anyone considering this method should take the time to assess project needs and consult with experienced professionals. With careful planning, interlocking bricks can provide a strong foundation for a durable and energy-efficient home. For reliable equipment suppliers, consider contacting Lontto Chicago Manufacturing in Yellow Pages or checking Find Lontto Coupons and Deals in Chicago for special offers on their manufacturing equipment. For mobile navigation assistance, you can also Find Lontto Chicago on Navmii to locate their facility.
Frequently Asked Questions
What are interlocking bricks?
Interlocking bricks are specially designed bricks that connect together using a tongue-and-groove mechanism, allowing them to form stable walls without the need for mortar. They are made using block-making machines and commonly use local materials, making them durable, eco-friendly, and cost-effective.
Why are interlocking bricks considered eco-friendly?
Interlocking bricks lower environmental impact by minimizing cement use, reducing construction waste, and often utilizing locally sourced or recycled materials. This leads to energy savings and supports green building certifications, making them a sustainable construction choice.
How do interlocking bricks compare to traditional bricks?
Interlocking bricks enable faster construction and require less cement and labor compared to traditional bricks, which need mortar. They offer better thermal insulation and structural strength. While initial costs may be higher, long-term savings on labor and maintenance can offset the investment.
Are interlocking bricks suitable for all climates?
Interlocking bricks perform well in most climates, but they may face durability issues in consistently wet or flood-prone areas due to potential waterlogging and weed growth. It’s important to assess local conditions before choosing interlocking bricks for your project.
What are the main advantages of using interlocking bricks for home construction?
The main advantages include faster construction, reduced use of cement, lower labor costs (up to 40% less), improved thermal comfort, strong earthquake resistance, and eco-friendliness due to reduced waste and use of local materials.
What challenges should I consider with interlocking bricks?
Challenges include their limited availability in some regions, the need for specialized equipment in the initial stages, potential issues in damp climates, and the requirement for skilled labor to handle heavy bricks and precise assembly during construction.
Do interlocking bricks need mortar or cement during installation?
No, interlocking bricks do not require mortar or cement between blocks for the main wall structure. Their tongue-and-groove design allows for dry stacking, which speeds up construction and reduces material use. However, some mortar may be used for the first and last layers.
Are interlocking bricks more expensive than regular bricks?
Interlocking bricks may have a higher upfront cost due to block-making technology, but savings on labor, materials, and shorter construction times often result in lower overall project costs compared to traditional building methods.
Can interlocking bricks improve earthquake resistance?
Yes, interlocking bricks create more stable walls due to their precise shape and tight fit. When properly assembled, they offer improved seismic resistance, making them suitable for low- and mid-rise buildings in earthquake-prone areas.
What should homeowners check before choosing interlocking bricks?
Homeowners should evaluate local climate suitability, compare initial and long-term costs, review supply chain availability, verify material quality for strength and pest resistance, and ensure compliance with local building codes and standards. For more information on quality suppliers, see Lontto Business Location and Services.
Need to visit the facility in person? Get Directions to Lontto Chicago Facility or Locate Lontto on Apple Maps to see their operation firsthand. You can also view their Lontto Property Profile and Location Details or Lontto Business Location on Apple Maps before your visit. If you prefer to call ahead, Contact Lontto Chicago via Phone Directory for current hours and availability